Guitars have been around for centuries, with a history that dates back to ancient civilizations such as the Greeks and the Romans. The modern guitar has evolved over time, from the traditional lute to the Spanish guitar and eventually the electric guitar. The art of guitar making is a complex and intricate process that has remained relatively unchanged for centuries, with the use of wood being a central component.For generations, luthiers have used select woods from various regions of the world for their guitars. The type of wood used can drastically affect the sound and overall quality of the instrument. The construction of a guitar requires various materials and tools such as braces, glues, clamps, sandpaper, and chisels. A successful guitar making experience also requires knowledge, patience, and a steady hand.
The Importance of Wood in the Guitar-Making Process
The wood used for the body of the guitar must be of high quality, and the selection of wood is crucial to the final sound and tone of the instrument. Different wood types such as mahogany, spruce, and rosewood can produce different sounds, and there are certain characteristics that luthiers look for, such as density and stiffness, which will determine the overall sound and durability of the guitar. Ultimately, it is the combination of wood types and the concert of various other elements like strings, pickups, and fretboards that will define the guitar’s tonal identity.When it comes to producing the guitar body, the luthier must first select the type of wood that they will use, as well as the design and measurements for the guitar body. The body typically consists of a top, back, and sides, which are glued together. The top is usually made of spruce, while the back and sides can be made from a variety of woods depending on the sound desired. Once the pieces are cut to size, they are carefully sanded and shaped to create the body’s distinctive look. Afterwards, bracing is added to the body for support and to enhance resonance. Many experienced luthiers will also tap and tune the wood to find its natural sound before proceeding with the construction process.
An array of specialized tools is used in the guitar making process. While some of the tools are standard carpentry tools like saws and planers, others are specific to guitar production, such as specialized clamps and jigs. The use of all these tools is necessary for the luthier to achieve perfect cuts and achieve the desired shape and contour of the guitar body. The sanding of the guitar body is a critical process that must be done with great care and attention to detail, as any slight deviation in the shape or contours can have a considerable impact on the sound and playability of the final product. The specific challenges and variations of guitar making have led to a subcategory of carpentry that calls for specialized knowledge and expertise. Creating a guitar is truly an art form that demands a fusion of technical know-how and artistic creativity.
Guitar Body Construction
The Anatomy and Structure of the Guitar Body
The anatomy of the guitar body can be divided into several key parts: the top, the back, the sides, the soundhole, and the bridge. The top, also known as the soundboard, is the most important part of the body as it produces the majority of the sound. It is usually made of solid wood, which is carefully selected for its resonance and appearance. The back and sides are also made of solid wood or laminate, with the former providing a more desirable tone. The soundhole is a hole located in the center of the top and is responsible for projecting the sound. Finally, the bridge is the part of the body that anchors the strings, providing a mechanism for adjustment of their lengths and intonation.
The Process of Crafting the Body: From Cutting to Assembly
The process of crafting the guitar body requires a combination of mechanical skill, artistry, and attention to detail. It begins with cutting the wood into specific shapes that will form the top, back, and sides of the guitar. Once the wood has been cut and the pieces have been assembled, the builder will then use various tools to shape the components into the desired form. This can include carving out the soundhole or creating the arch of the back. After the shaping is complete, the body is glued together and left to dry. Once it has dried, the body is sanded and finished with a stain or other coating to protect the wood and enhance its appearance.To create a quality guitar, it is important to consider every aspect of the instrument, including the neck. The neck plays a key role in the instrument’s playability and overall sound, as it influences the strings’ tension and the position of the frets on the fretboard.
Crafting the Guitar Neck
The Importance of a Quality Neck for Sound and Playability
The importance of a quality neck cannot be overstated when building a guitar. It affects the sound, the playability, and the aesthetics of the instrument. The neck is usually made from a single piece of wood, which can be either bolted to the body or glued on. The most commonly used woods for necks are maple and mahogany, but some luthiers also use rosewood or other exotic materials. The shape and contour of the neck also play a huge role in the feel and comfort of the guitar, so many different shapes and profiles are available to ensure the perfect fit for every musician.
The construction of the neck begins with selecting the right piece of wood, which needs to be dried and properly seasoned to ensure stability and resistance to warping. Luthiers will then shape the neck, usually using specialized planes and saws, and install a truss rod inside to add strength and stability. The fretboard is then installed on top of the neck, and the frets are inserted and leveled. Finally, the neck is sanded down and sealed with a finish that complements the guitar’s overall aesthetic.After the neck is completed, it is attached to the body of the guitar. Joining the neck and body can be done in several ways, including a bolt-on method, where the neck is bolted to the body, or a set-neck method, where the neck is glued to the body. Both methods have their advantages, and the choice usually depends on personal preference, the type of guitar, and the intended sound.
Once the neck is attached, the guitar hardware and electronics can be installed. This includes the bridge, tuners, pickups, volume and tone knobs, and wiring. It’s important to carefully install the hardware in the correct positions for optimal sound and playability. The wiring must also be done correctly, with attention to detail to avoid damaging the guitar or producing unwanted noise.
The final step in guitar making is finishing. This includes sanding the body and neck to a smooth finish and applying a protective coating or paint. A high-quality finish not only adds aesthetic value but also helps protect the guitar from damage and moisture. Different finishes can also affect the sound of the guitar, so careful consideration is necessary when choosing the type of finish to apply.
Guitar Assembly and Finishing
The Art of Gluing and Joining the Body and Neck
Once the body and neck are prepped and ready, the next step is assembly. The sides of the guitar body are glued to the back, and the sides are then attached to the soundboard. The neck is attached to the body with a well-fitted joint. It is essential to ensure a tight joint to prevent any movement or shifting that can affect the tone or playability of the guitar. After the base assembly, work continues with hardware installation and electrical work. The hardware includes bridges, tuners, and pickguards. The electrical components of the guitar include pickups, potentiometers, and output jacks.
The Final Touches: Hardware Installation and Electrical Work
The final touches of guitar making are just as important as all the previous steps. The finish of a guitar can make the difference between a good sound and a great one. Sanding and polishing the guitar’s body and neck take time and effort; however, these steps can be rewarding if done correctly. The final finish should have no bumps, bubbles, or uneven spots. Once the finish is complete, the guitar is ready for testing. The final test involves playing the guitar to ensure that the sound is rich and full. If everything sounds great, the guitar is ready to be gifted, sold or kept for personal use.
The Importance of Finishing: From Sanding to Polishing
Finishing is an essential part of guitar making, and it deserves just as much attention as any other step. The surface and shine of the guitar should make the instrument stand out. It should be admired from a distance and admired even more when played. The finishing touches make the entire building process worth it. Finally, guitar enthusiasts and players who appreciate the guitar-making process will tell you that picking up and playing an instrument that you built with your own hands is a feeling that cannot be matched.
Conclusion
In conclusion, the process of crafting a guitar is a detailed and intricate art form that requires patience, precision, and dedication. Every step of the process, from selecting the right pieces of wood to the final finish, contributes to the sound and feel of the instrument. While the process itself may be challenging, the end result is always rewarding. Whether it’s for personal use or for sale, building a guitar grants the satisfaction of having created something beautiful and meaningful that can last a lifetime. Indeed, the art of guitar-making continues to thrive and evolve, and the passion for this craft can be seen in the countless guitars that are being played and loved across the globe every day.
Aspiring luthiers or guitar enthusiasts who want to delve into this craft should take the time to research and learn about the process in detail. There are many resources available online, including instructional videos, forums, and blogs, that can provide invaluable guidance and advice. Additionally, there are luthier schools available for those who want to pursue this art form as a profession. Overall, building a guitar is a unique and enriching experience that combines creativity, technical skills, and a love for music. A beautifully crafted guitar is more than just an instrument – it’s a masterpiece that tells a story and captures the essence of its maker and player.Guitar making is a fascinating art form that has been honed and practiced for hundreds of years. Craftsmen have dedicated their lives to creating beautifully crafted instruments that produce outstanding resonance and sound quality. Every aspect of guitar making, from selecting the right materials to finishing touches, requires meticulous detail and passion. Aspiring luthiers and guitar enthusiasts can learn about the craft through instructional videos, forums, and blogs available online. Building a guitar produces a sense of pride and accomplishment, as every guitar tells a unique story about its maker and player.
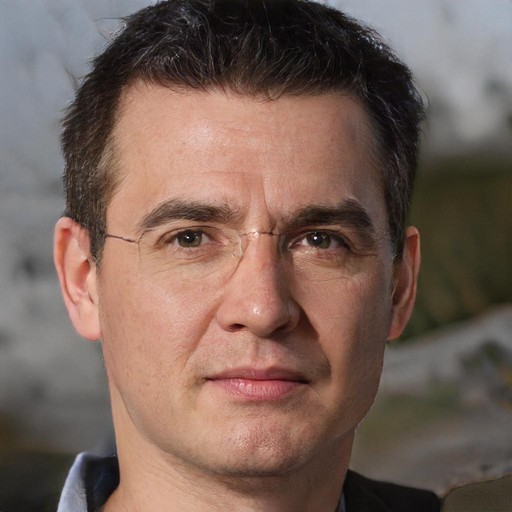
Hi there! I’m Casey Marshall, a guitar enthusiast and repair specialist. With years of experience playing and repairing guitars, I’ve developed a deep understanding of the instrument. Through this blog, I share tips and advice on guitar repair and maintenance, as well as insights into the world of guitar playing.